General Information
Silicone foam is a synthetic rubber product used in gasketing, sheets and firestops.
Features
Silicone sponge sheeting is used for a variety of purposes, including sealing, cushioning, vibration dampening, and thermal insulation. Some specific applications of silicone sponge sheeting include:
Gaskets and seals: Silicone sponge sheets are used to create airtight and watertight seals in various industries, such as automotive, aerospace, and electronics. They provide excellent resistance to weathering, UV radiation, and extreme temperatures. See our Custom Cut Gaskets & Seals page.
Cushioning and shock absorption: Silicone sponge sheets are used as padding or cushioning material in packaging, electronics, and medical devices. They can absorb shocks and vibrations, protecting delicate components or products during transport or use.
Thermal insulation: Due to their low thermal conductivity, silicone sponge sheets are used to insulate and protect components that are exposed to high temperatures, such as in industrial ovens, furnace seals, or engine gaskets.
Sound dampening: Silicone sponge sheets can be used as soundproofing material in various applications, including architectural settings, automotive industry, or HVAC systems. They can reduce noise transmission and improve acoustic isolation.
Overall, silicone sponge sheeting is a versatile material with numerous applications where properties like flexibility, high-temperature resistance, and sealing capabilities are required.
Electrical insulation: Silicone sponge sheets are used as electrical insulators due to their excellent dielectric properties. They can be used to cover electrical wires or components, providing protection against electrical shocks or short-circuits.
Form And Usage
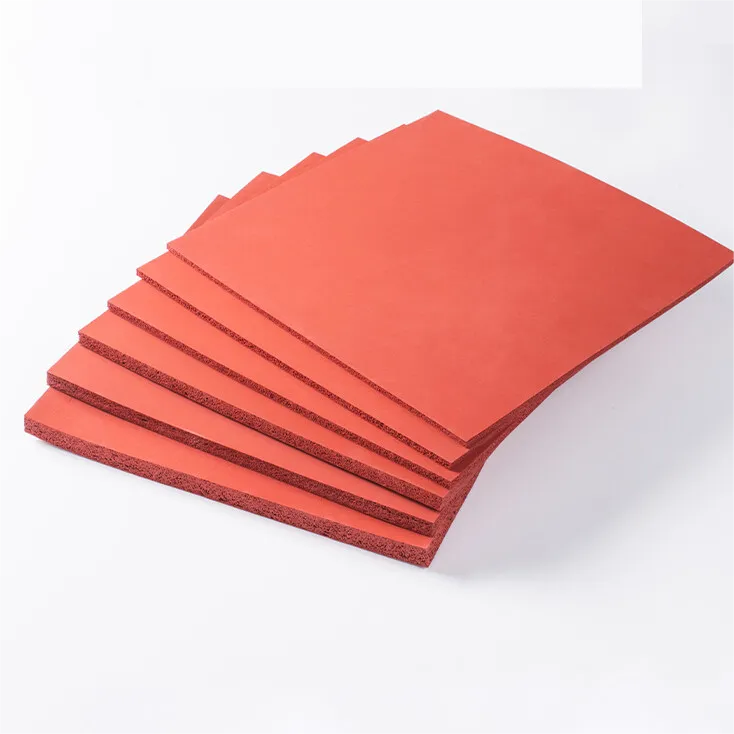
Silicone Foam Sheet
◆ Gaskets and seals
◆ Cushioning and shock absorption
◆ Thermal insulation
◆ Sound dampening
◆ Electrical insulation
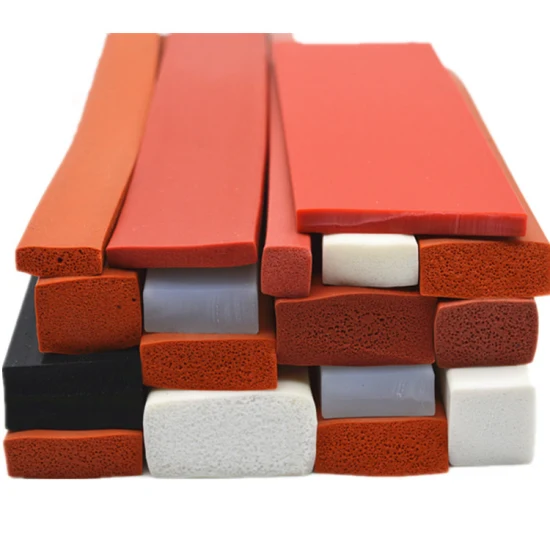
Silicone Foam Strip
◆ Cushioning and shock absorption
◆ Thermal insulation
◆ Sound dampening
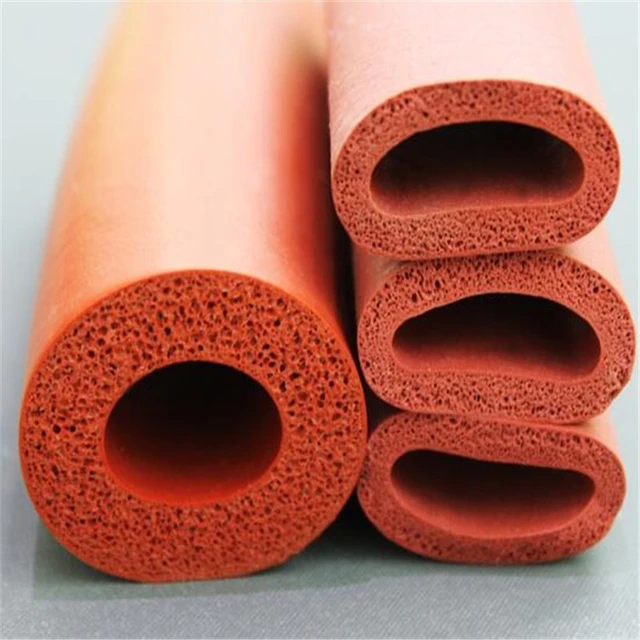
Silicone Foam Strip
◆Thermal insulation
◆Vibration damping
◆sealing flexibility
◆Insulation
◆Noise reduction
Application Fields
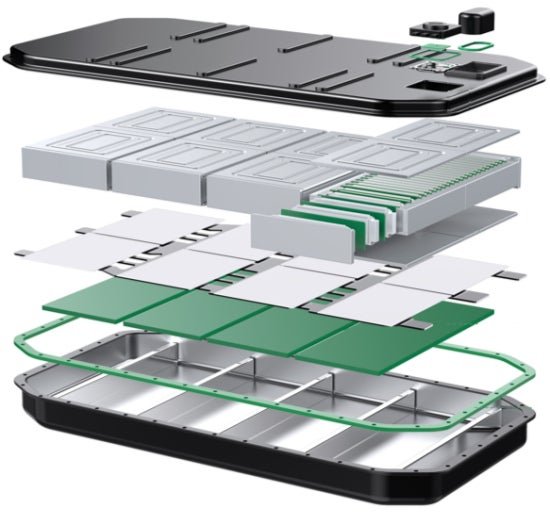
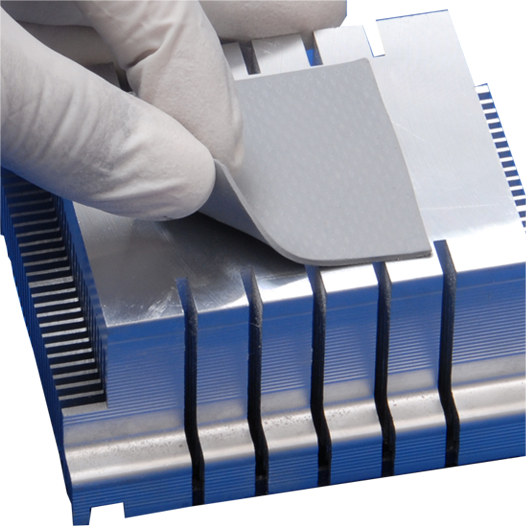
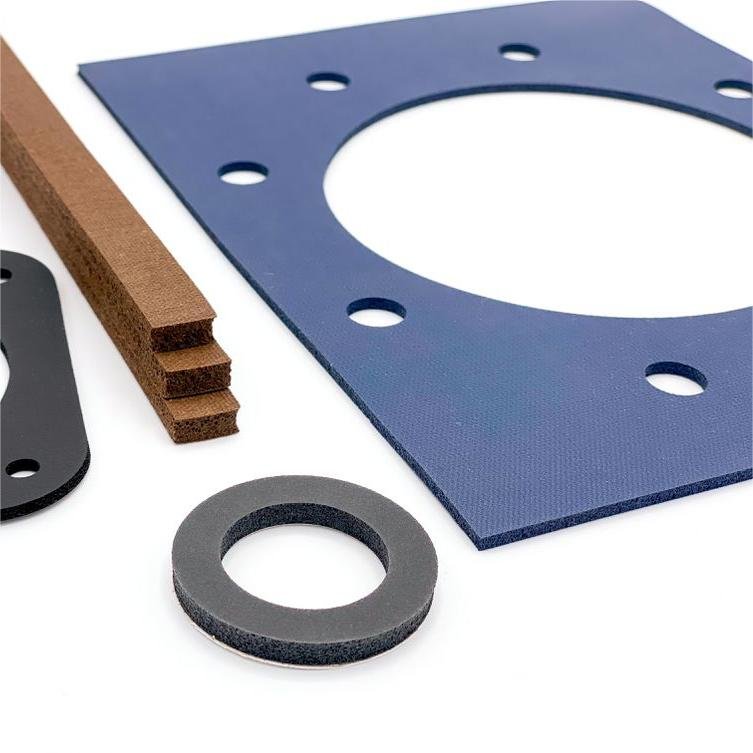
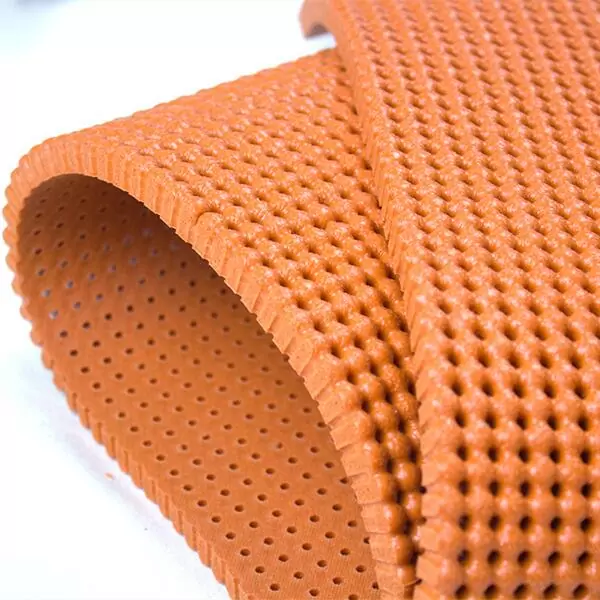
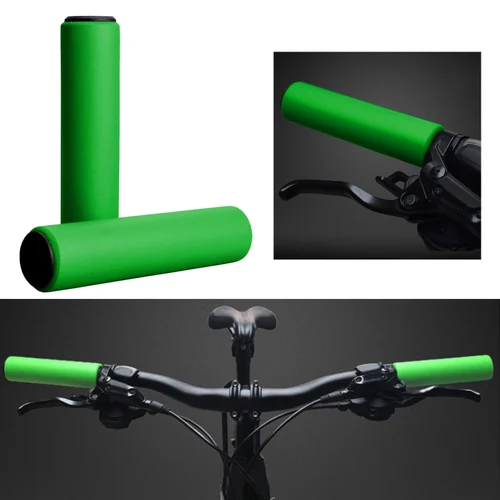
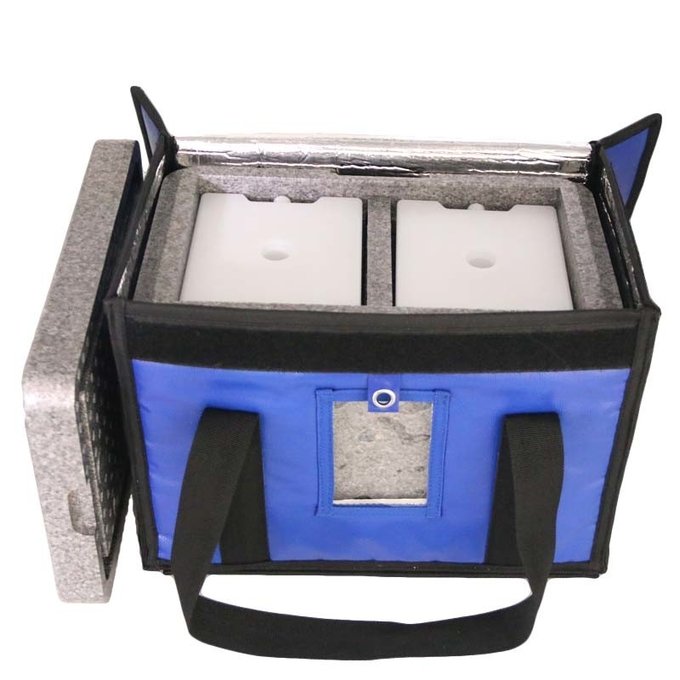
Manufaturing/Processing
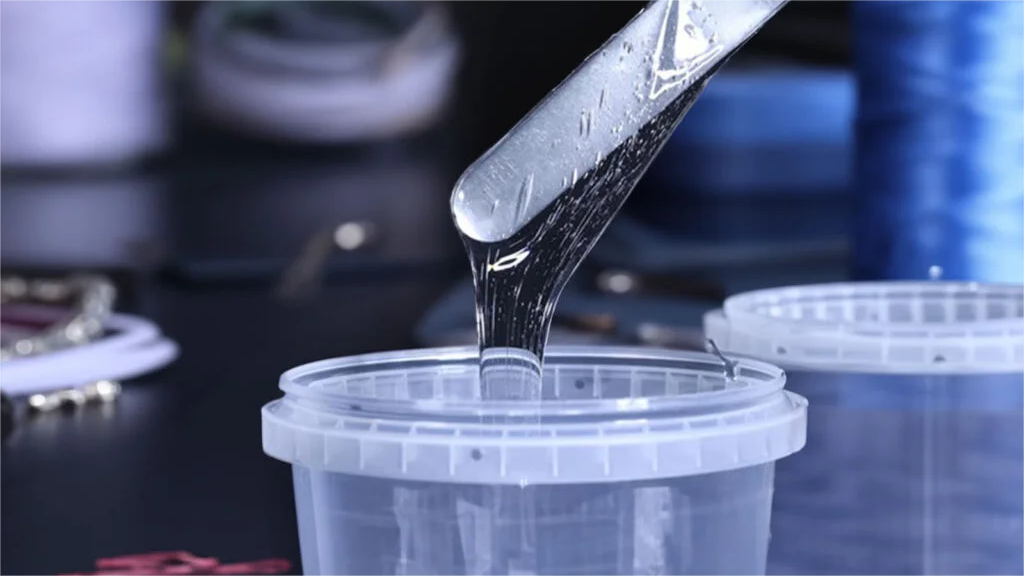
Material
Silicone Foam is made of liquid silicone rubber and foaming agent
Silicone Material: The composition of the liquid silicone rubber (LSR), including the base silicone material and curing agent, affects the foam properties.
Foaming Agent: Type and concentration of the agent, as well as its general compatibility with silicone.
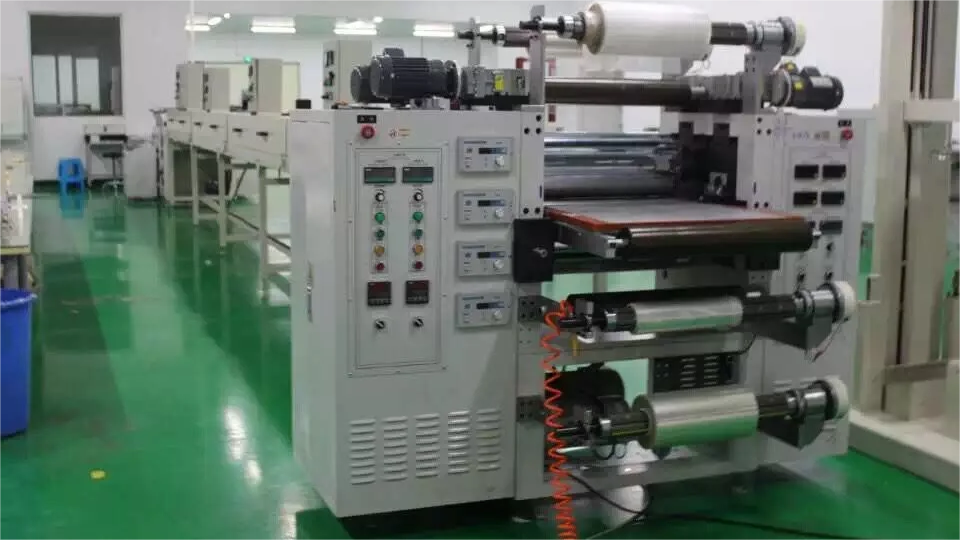
Calendering (Silicone Foam sheet)
1. Material preparation: Mix Liquid Silicone Rubber and the Curing agent, adding foaming agent. Vaccuming the material.
2. Calendering:Direct material through single or multiple pairs of heated hard steel rolls useing calendering machine
3. Curing: Heating curing on the conveyor belt.
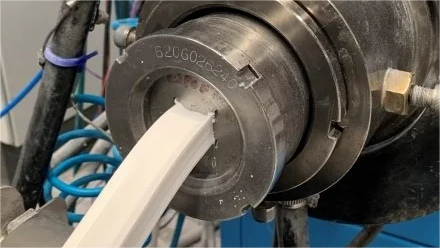
Silicone Foam Extrusion (Silicone Foam strip)
1. Material preparation: Mix Liquid Silicone Rubber and the Curing agent, adding foaming agent. Vaccuming the material.
2. Die Design: An extruded material is shaped by a die, which is a specialized instrument.
3. Heating and Curing: The silicone material is heated as it passes through the extruder, cause the material to form.
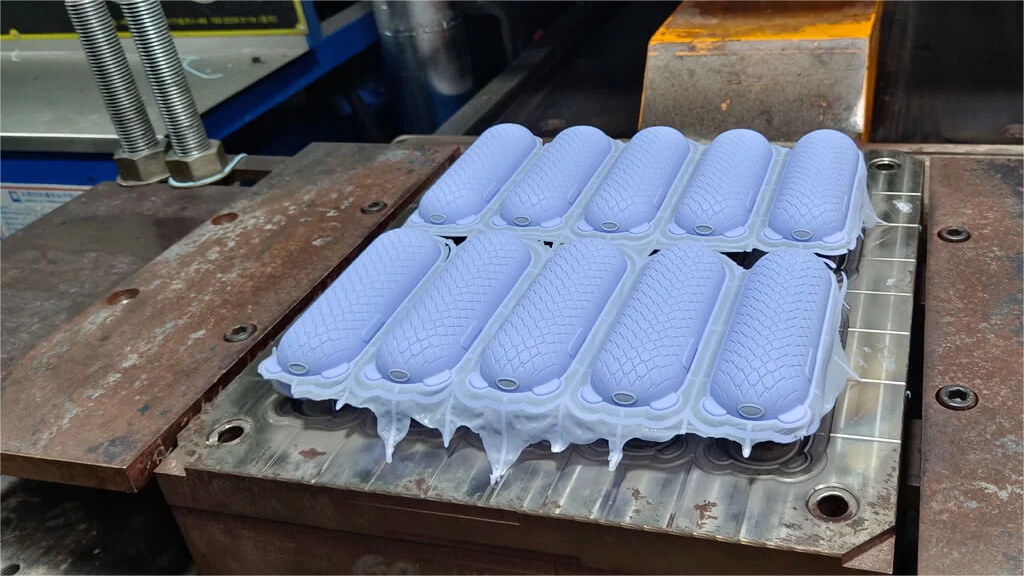
Silicone Foam Molding (Specific Shape)
1. Mold Preparation: Preparing mold and apply mold release agent in the surface of the mold.
2.Material preparation: Mix Liquid Silicone Rubber and the Curing agent, adding foaming agent. Vaccuming the material.
3. Mold Filling: Pour the mixed silicone material into the mold.
4. Curing: Apply correct curing tempeture and curing time to wait till the product is formed.
5. Cooling and Demolding.
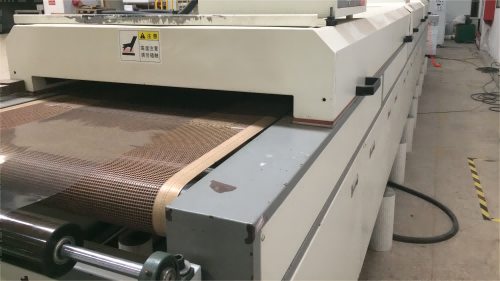
Silicone Foam Coating (Fabric or Anti-slip use)
1. Material preparation: Mix Liquid Silicone Rubber and the Curing agent, adding foaming agent. Vaccuming the material.
2. Glassfiber, fabric preparation.
3. Pouring the silicone rubber material on the surface of the fabric or glass fiber.
4. Calendering, use roll to press specific pattern.
5. Curing: In between the heating tunnel, the material curing processing.
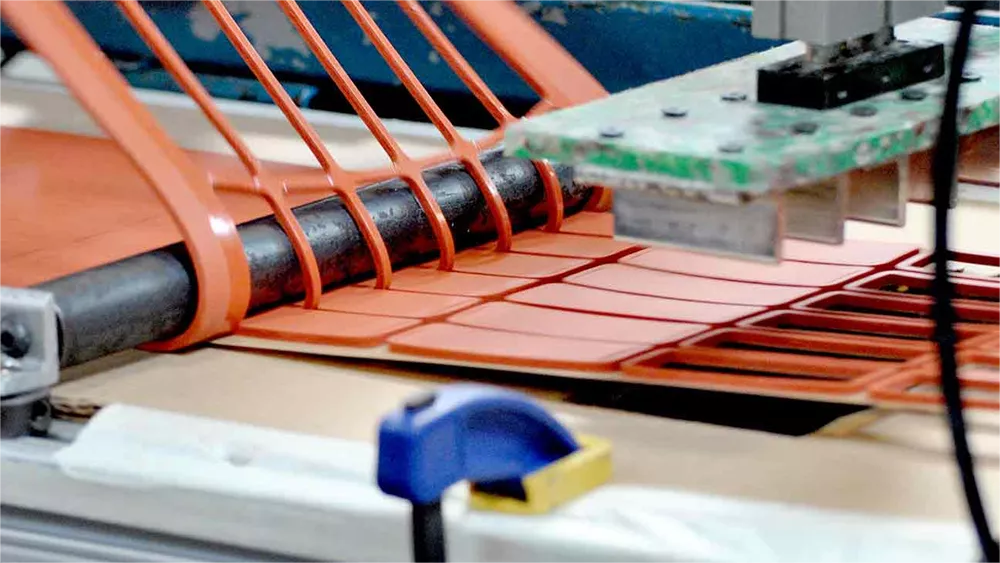
Die cutting
1. Mold Design.
2. Process the cutting using the cutting mold.