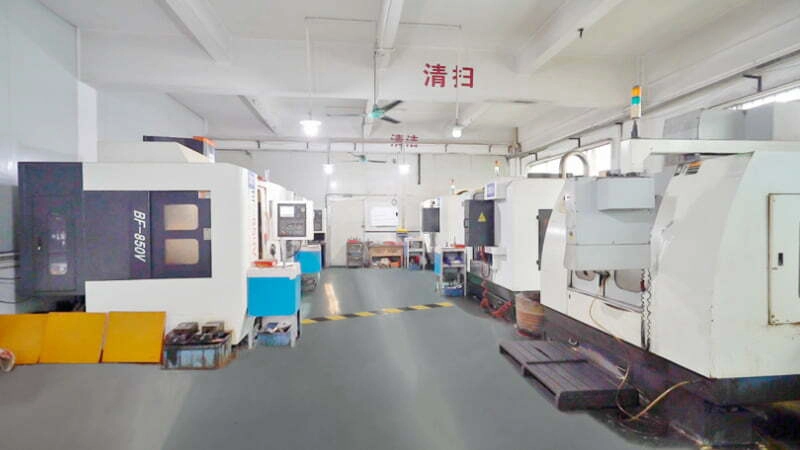
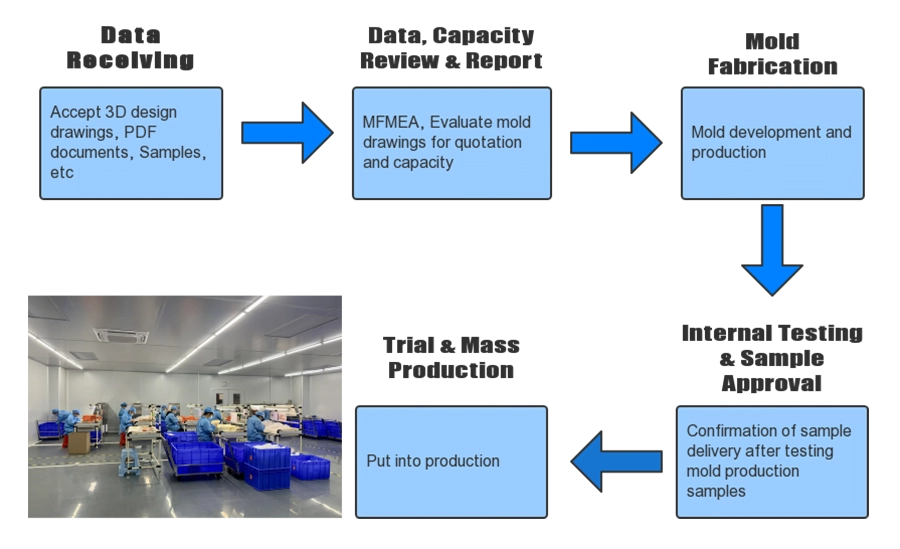
Liquid Silicone Rubber Mold with Cold Runner (Needle Valve)
Liquid Silicone Rubber Mold, also called LSR Mould or Silicone Injection Mold, has some types according to liquid silicone rubber materials feeding systems, the silicone materials state, mold runner systems silicone molded machines types, etc.
Actually, for mass production and precision liquid silicone molded parts or products, silicone mold manufacturers or customers mainly choose liquid silicone rubber injection molding with shut-off & needle valves, which can save lsr materials, have long mold lifetime, more precision and easy to automatic production etc.
LSR Silicone Injection Mold:
Following mainly talking about liquid silicone rubber injection mold with needle valves & silicone injection mold designs。
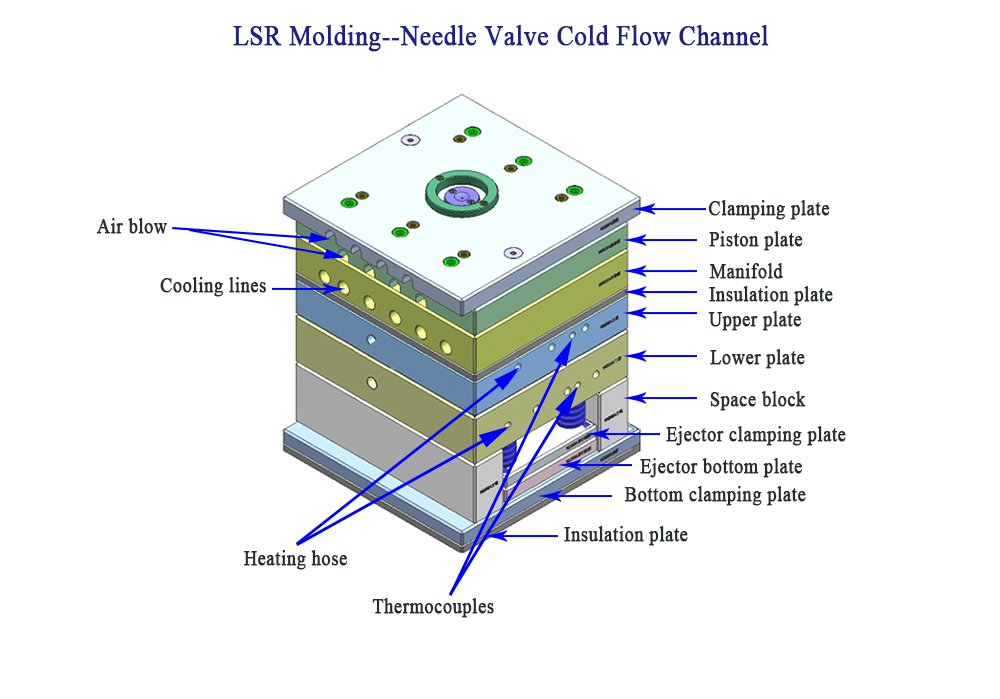
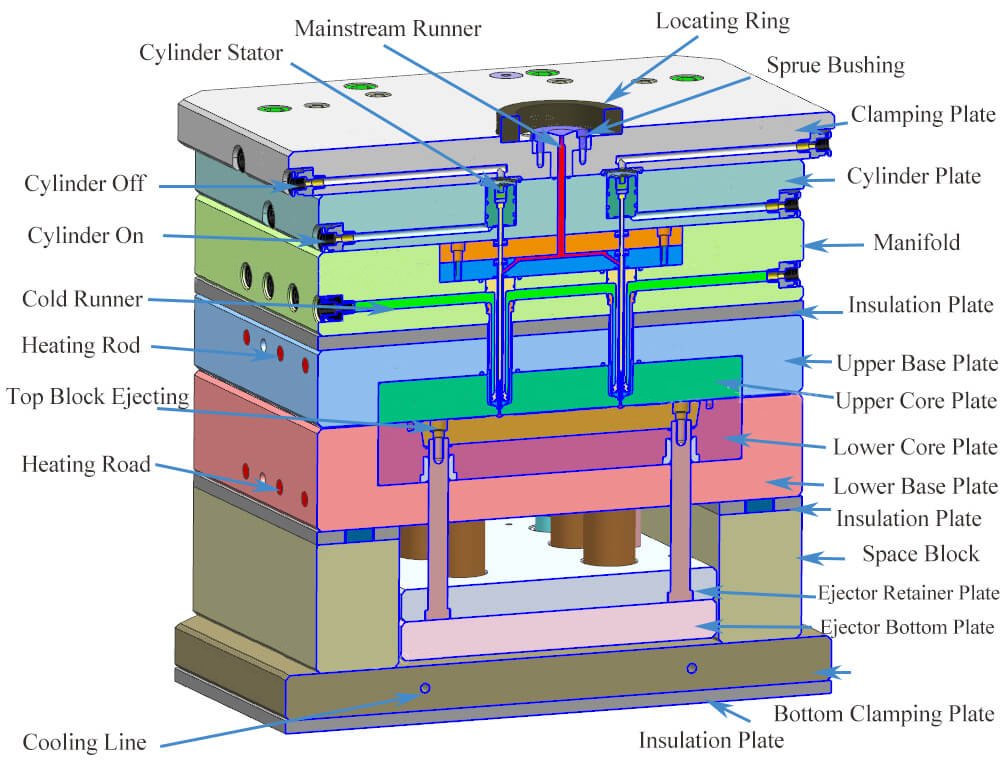
Two different types of LSR injection machines and liquid silicon injection molded designs
1. Vertical LSR Injection Machines and Mold Designs:
This kinds of LSR injection mold & machines mainly designed for 2-shot & liquid silicone rubber overmolding, like liquid silicone rubber overmold with plastic, metal or glass, or two different LSR color, handness or silicone materials etc.
liquid silicone rubber for overmolding silicone membrane Rubber To Metal Bonding
2. Horizontal LSR Injection Machines and Mold Designs
Horizontal Liquid Silicone Rubber Injection Machines, like plastic injection mold, which easier to achieve automated production.
LSR Injection Mold
Horizontal Liquid Silicone Rubber Machine
Silicone Injection Molding manufacturing process
Notes: Common compression machines also can converted into LSR machines only change materials feeding systems, which only produce some LSR products & parts as not high tolerance demands of sizes or designs, like baby care products, packaging products or cosmetics etc. This kind LSR molding is cheap, similar to silicone rubber compression molding or rubber tranfer molding.
LSR Injection Molding Designs, is something like plastic injection molding with or without hot runner systems. LSR injection molding with shut-off valves, also called cold runner systems, which can save liquid silicone rubber materials and labor cost, also have good LSR product’s surface (small injection gate). Liquid Silicone Rubber Injection molding without shut-off valves, like silicone injection molding, also called hot runner LSR & direct gate liquid silicone rubber injection molding, which can save some mold cost but bigger injection gate (not good lsr product’s surface)
Liquid Silicone Rubber Mold with Hot Runner
Liquid Silicone Runner Injection Mold without shut-off valve &needle valve,also called hot runner systems LSR injection mould,which designed for big Isr silicone molded products like liquid silicon bottle &cups shapes,not high precision liquid silicone parts,or like liquid silicone pour-into only for samples or low-volume production,in aim to save liquid silicone mold-making cost.
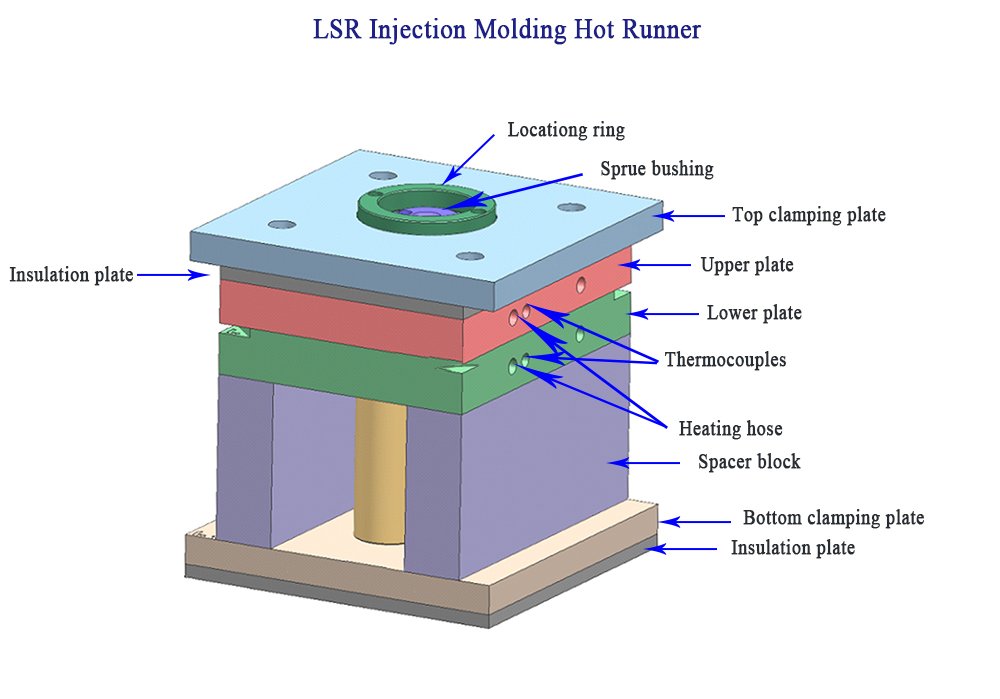
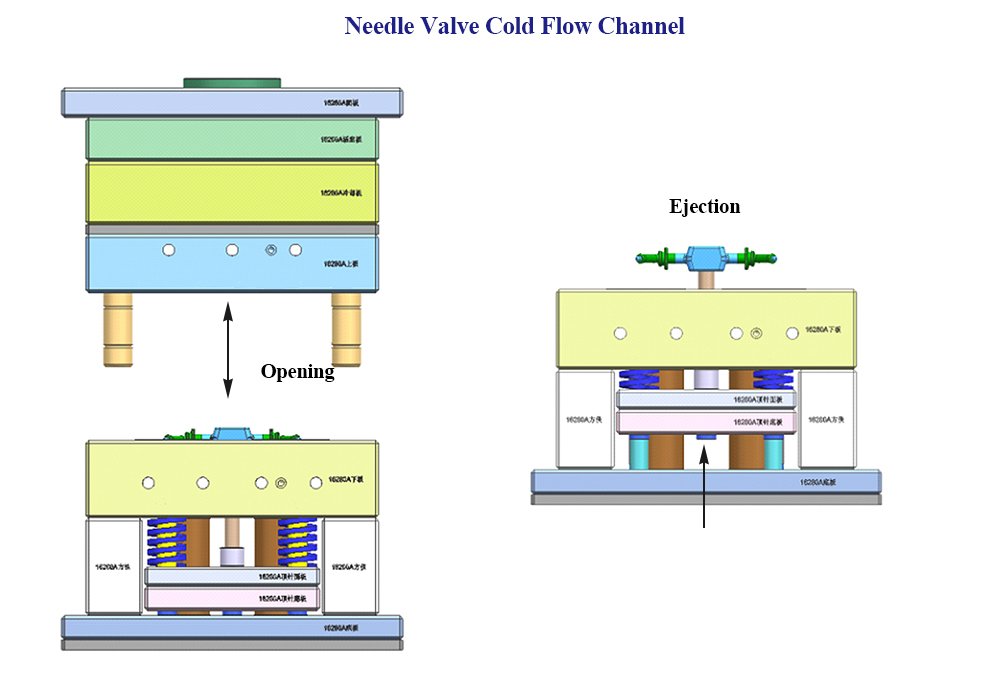
Different LSR Molding Process -Converted LSR Mold by Compression Machine
Converted LSR Silicone Mold By Compression Machines
Compression machines also can be converted into liquid silicone molded machines only add LSR material feeding systems, which only produce some LSR products &parts as not high tolerance demands of sizes or designs,like baby care products,packaging products or cosmetics etc.
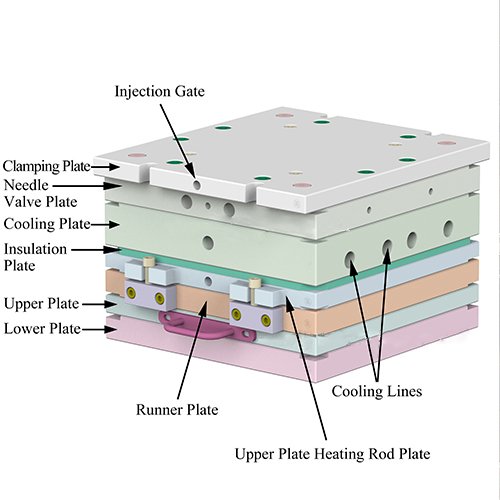
This kind LSR molding is cheap,similar to silicone rubber compression molding or rubber tranfer &injection molding.
Notes:This kinds of LSR Silicone Mold,called false LSR mold or false silicone injection mold, as have many “sequela” like: short mold life, rough design &sizes tolerance be restricted by mold structure, and also can’t produce complicated-design Isr silicone products.
Converted LSR Silicone Molded Methods
Liquid Silicone Rubber Mold Design for Manual Liquid Silicone Materials Feeding
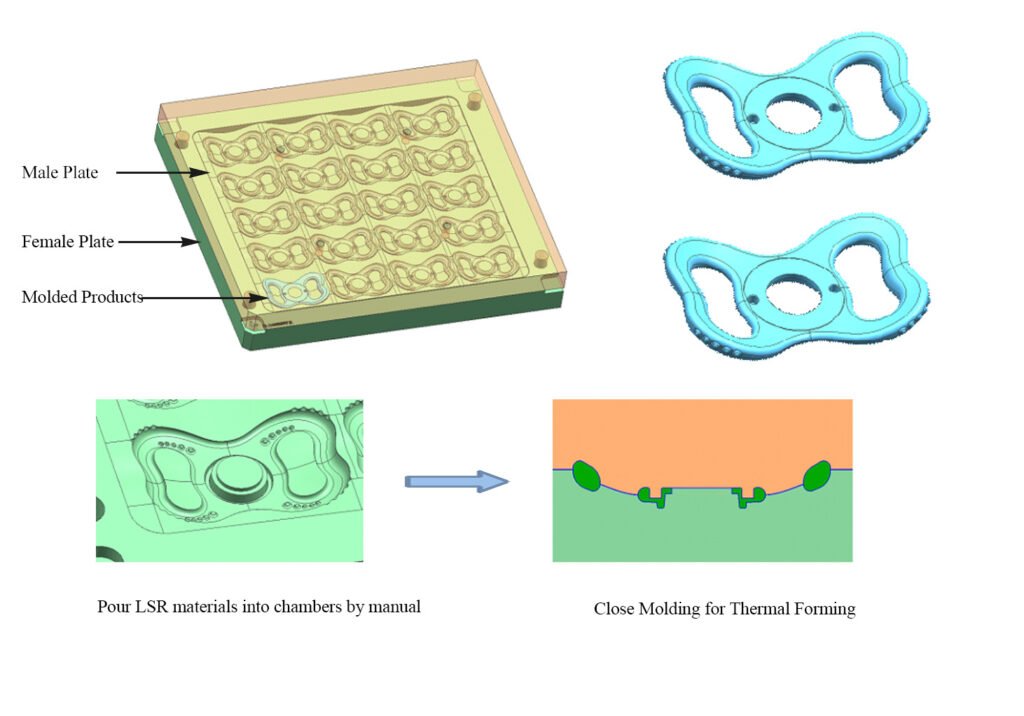
Silicone Rubber Transfer Molding
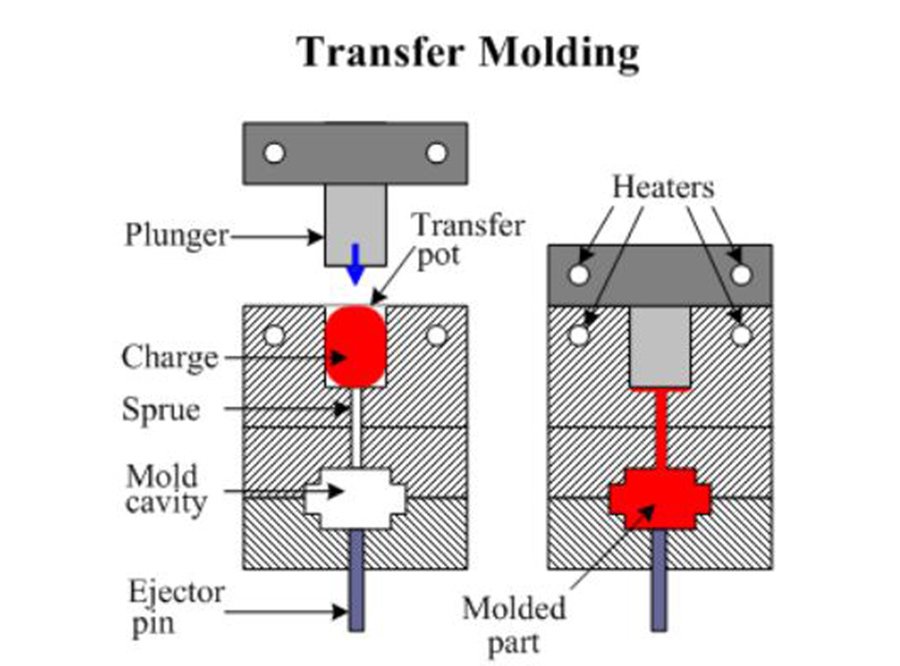
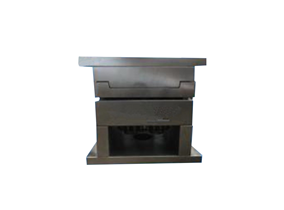
Liquid Silicone Rubber Transfer Molding & Silicone Injection Mold
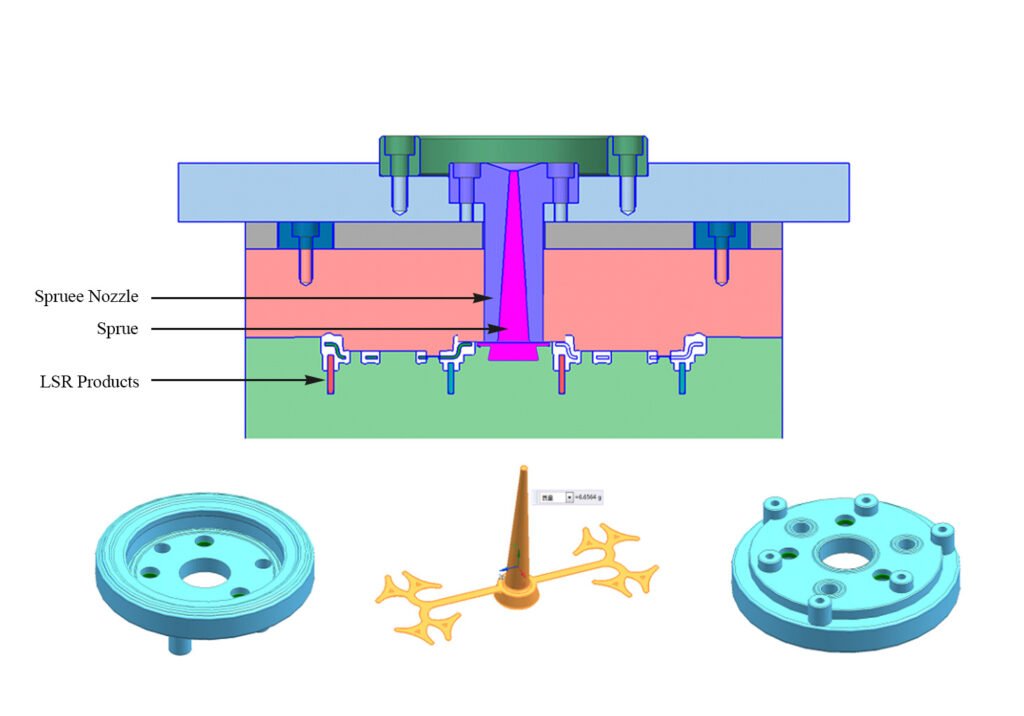
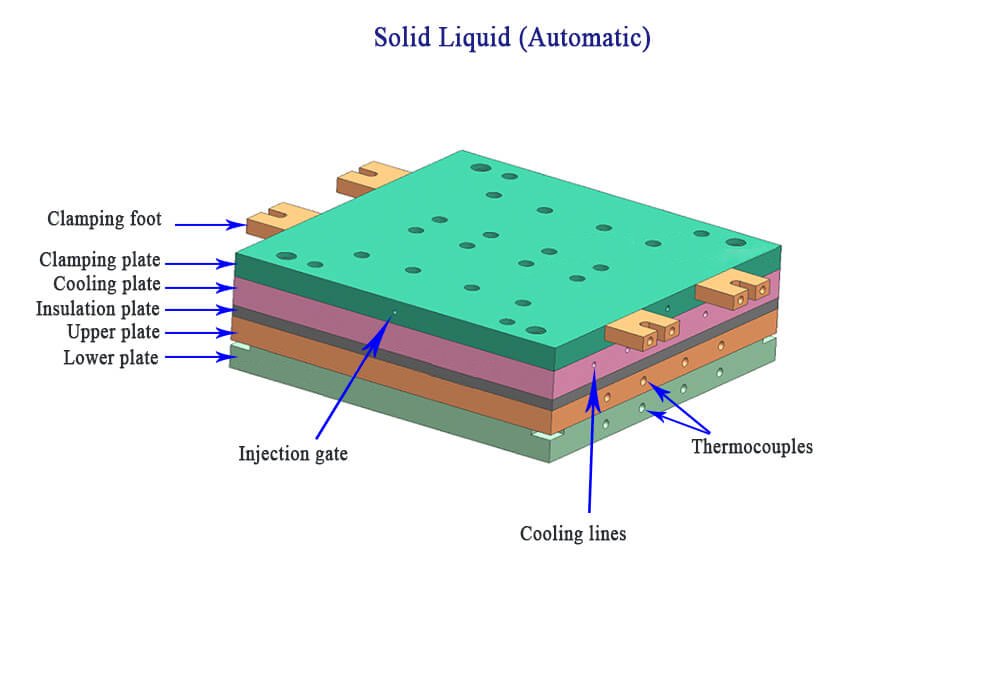
Liquid Silicone Runner Injection Mould Know-How
Liquid silicone rubber injection molding is the most precise,efficient,and safest and manufacturing process,the products by LSR injection molding with mini parting line and no and less silicone rubber burrs.
Wall Thickness:
Because liquid silicone material doesn’t sink like plastic,so it’s wall thickness does not
have to be uniform.The wall thickness can be as thin as possible with silicone molding, can down to 0.127mm
Tolerance and Molded Part Shrinkage:
Part shrinkage will effect tolerance of products directly.The shrinkage variations of liquid silicone can be little compared to plastic material,so the tolerance of LSR can be much closer. Sizes tolerance can less +/-0.02mm
Shrinkage:
It occurs during molding and post curing or unit fully cross-linked.
It depends on different materials.Typical shrinkage is between 1%and 5%.
Varies by the manufacture and product range from 0.25 per inch.
Optical Properties:
Liquid silicone is optically clear and have higher surface finishes compared to typical glass,and is widely used as optical lens.Some silicone refractive index can equal that of glass (1.53).what’s more,the silicone optical lens are UV aging,can operate at high temperatures,and have wider spectrum of transmission compared to acrylic and polycarbonate.
Radiu and Fillets:
Radiu and fillets not only can improve a product’s appearance but also increase it’s tear strength.
Surface Finish:
Surface finish can match the mold texture.Surface finish can be dull,shiny,or include part identification marks.Surface finish has a direct bearing on the coefficient of friction.
Usually, textured surfaces provide better part releases than polished surfaces when molding.
Draft Angles:
Draft angels are not required for silicone parts but for plastic part.
Undercuts:
Undercuts is available on de-formable products.The products can be stretched to remove from cores without any deforms.Some times,we will add release agent to assist in expanding products to remove from cores.Note:usually,undercuts do not require expensive slides for the mold.
Parting Lines and Gate Location:
Liquid silicone are flexible,have small parting line,and can make the parting line at a suitable location compared to solid silicone and plastic.
MOLD DEVELOPMENT PROCESS
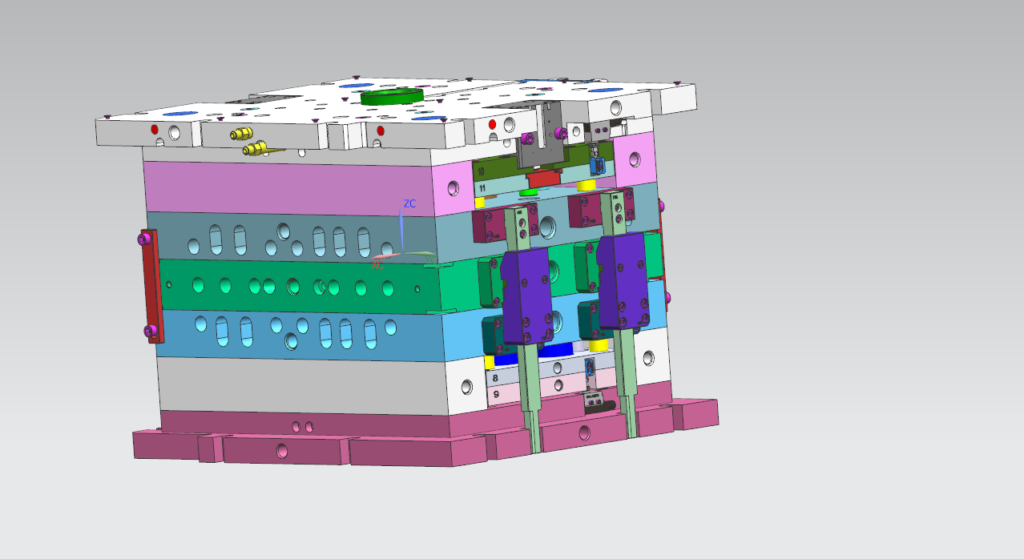
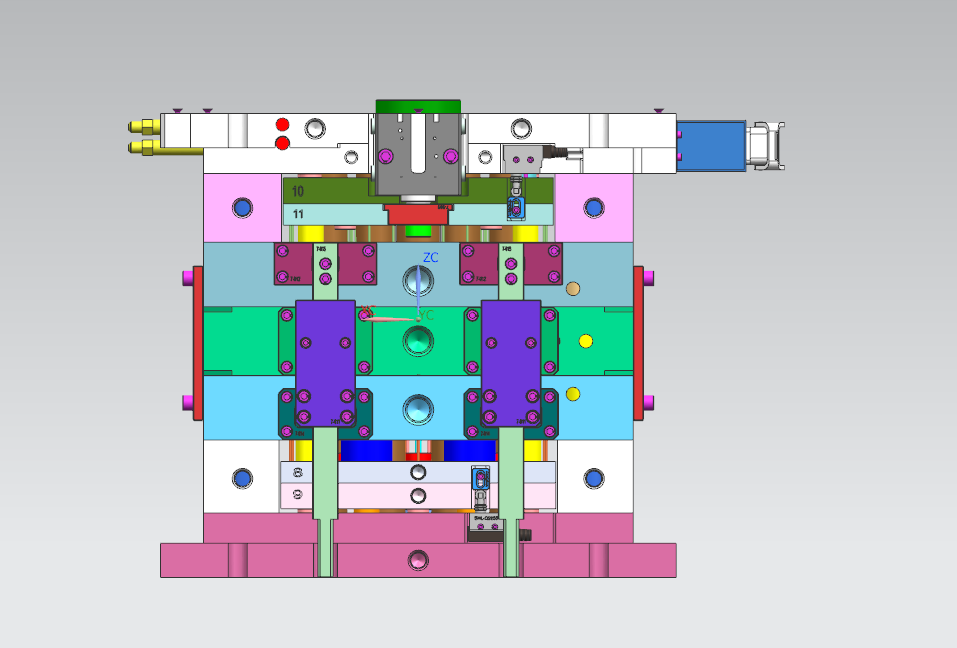
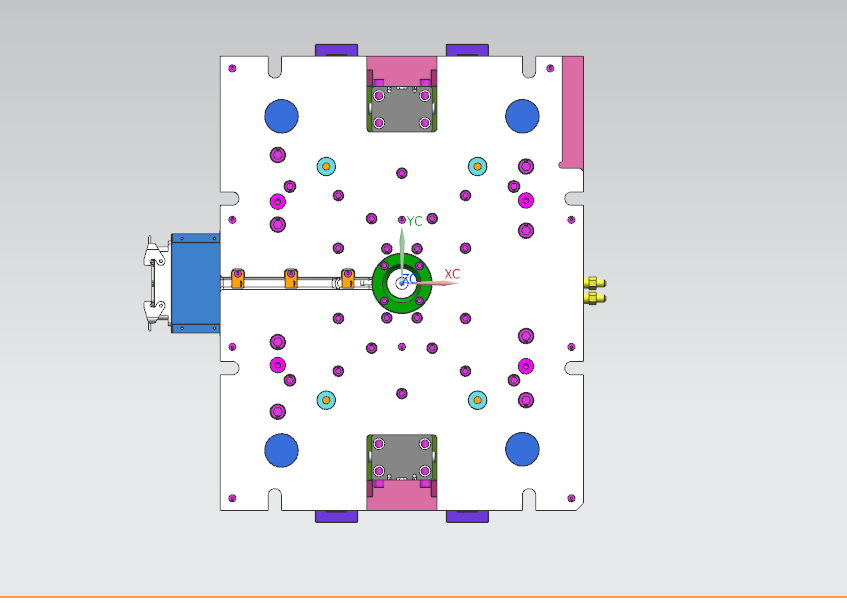
As a quality custom silicone mold manufacturer, we have over 18 years of experience providing custom silicone kitchen products and silicone compression molding services.
We have more than 30 professional machines (molding machine, injection molding machine, liquid injection machine) and more than 20 supporting machines (air compressor, punching machine, CNC secondary curing oven, tunnel oven, printing machine); our annual output value is nearly 80 million RMB.
Step 1: Data Receiving
Accept 3D design drawings, PDF documents, Samples, etc.
Step 2: Product Solutions
1. Data Review & MFMEA 2. Tool Conception Report 3. Capacity Review & Quotation After the technical review of the design drawing, the mold-making plan and the evaluation of the production capacity will be obtained.
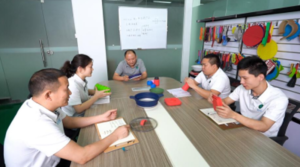
Step 3: Tool Fabrication
In mold development and production, our professional design team ensures accuracy and professionalism.
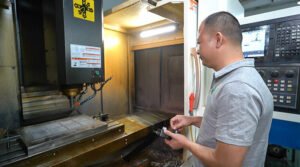
Step 4: Internal Testing & Sample Submission
Confirmation of sample delivery after testing mold production samples, we provide customer satisfaction with customized solutions.
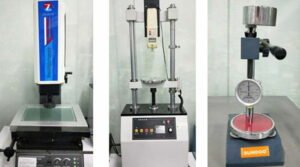
Step 5: Trial Run & Trial order
Over 18 years of R & D experience of the professional development team, we provide personalized customization, and one-stop service solution to fulfill customers’ requirements.
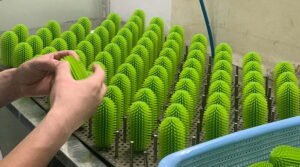
Step 6: Mass Production
With 30 sets of molding machines(compression, LSR injection, plastic injection ), 20 sets supporting advanced machines (air compressor, CNC secondary curing furnace, etc), all are Dust-free workshops and strictly QC procedure, which ensure accurate production and efficient delivery.
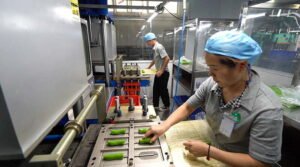
Step 7: Warehouse And Logistics
We have a separate warehouse for storing products prior to dispatch. We will also help our customers with the required logistics if required.
Step 8: After-Service
We want all the goods we deliver to our customers to be of high quality and to meet your needs. If there are any problems, please contact our sales or customer service within 24 hours.
Description
The mold department is fully equipped with a series of precision equipment, which is a collection of research and development, design, and production integration company, in order to achieve the design concept, independently set up the mold development, with CNC and a variety of precision equipment, from the design concept to the physical sample has an independent and efficient mode, perfectly guarantee the timeliness of the product on the market!
Safety
WS silicone products have been appreciated and supported by many customers for nearly 20 years, and all products are made of 100% food-grade and odorless raw materials and high-end machines. We have established a professional and complete manufacturing system, using various types of production equipment, with a number of product inspection procedures, including 4 manual professional inspections, to ensure that there is no flaw in product quality in terms of quality control. At the same time, our factories continue to pass BSCI and ISO certifications, and our products have more safety certifications, such as FDA, LFGB, and so on.
Quality
In terms of raw materials, we choose the world’s top raw materials, such as Wacker, Shin-Etsu, etc., which have heat resistance, cold resistance, weather resistance, chemical stability, transparency, and colorability. Products are in a leading position. During the production process, all workers agree to wear clean clothes, disposable clean shoe covers, clean caps, and masks to ensure that the products are kept clean during production and inspection. During the production process of the product, there is pressure, Post-Cure, and four professional inspections, and the production is completed after strict packaging.
Process
For a better purchasing experience for customers, the order placing process set by our company is extremely convenient. If you need to make customized products, you can provide the following materials: 3D design drawings/PDF documents/Samples, if not, you can provide specific parameters and pictures, we will conduct a technical review, mold production plan, and capacity evaluation. After confirmation, the order can be placed into mass production.